RESOURCES & DOWNLOADS
- Open Face (pdf)
- Crossdraft (pdf)
- Modified Crossdraft (pdf)
- Side Downdraft (pdf)
- Full Downdraft (pdf)
- Paint Mix Room (pdf)
- FLO (pdf)
- Batch Non-Recovery Booth (pdf)
- Batch Cartridge Recovery Booth (pdf)
- In-Line Process Recovery Booth (pdf)
- Powder Recovery Collectors (pdf)
- Reclaim Module (pdf)
- Manual Wash Enclosure (pdf)
- Media Blast Booths (pdf)
- Dust Collectors (pdf)
- Batch Oven (pdf)
- Powder Coating Ovens (pdf)
OSHA 1910.107
Spray finishing using flammable and combustible materials.
https://www.osha.gov/laws-regs/regulations/standardnumber/1910/1910.107
Summary:
This code is from the Occupational Safety and Health Standards subpart 1910 Hazardous Materials and applies for Spray finishing using flammable and combustible materials. It covers the construction materials of the spray booth structure's functioning components as well as the locations and requirements of noncombustible materials and filters. The interior surface of the booth and floor are specified to prevent accumulation of residue for ease of cleaning safely and to be noncombustible.
Baffle plate usage and safety requirements, Illumination of the booth is specified for conditions that effectively provide light safely, dry type overspray collectors or exhaust air filters and are specified for placement locations and discarding procedures. Filter combinations with alternative components are also discussed. All electrical equipment and related including electrostatic apparatus, lamps, portable lamps, grounding conformance. Drying, curing, and fusion apparatus specifications are included as well as Powder-coating equipment requirements. Other specifications include minimum separation for hot surfaces, wiring type, wiring conformance, grounding requirements for all metal parts of the spray booth such as the exhaust duct, piping systems conveying flammable liquids or aerated solids. Air ventilation, exhaust systems, and piping requirements are specified. The fire protection section includes sprinkler system cleaning, fire extinguishers, grounding containers for prevention of spark discharge and valve access. Distances between painted goods are established and maintained.
NFPA 33
Standard for Spray Application Using Flammable or Combustible Materials
This standard provides requirements to mitigate fire and explosion hazards of spray application processes that use flammable or combustible materials.
Summary:
The current, 2018 edition of this standard delves into safe use of flammable or combustible material used in spray applications. Building off other NFPA, ANSI/UL, and ASTM/ASME documents, this standard outlines safety means to control and confine combustible material and limit the potential for fire or explosion. This applies to the average use of flammable or combustible mists, vapors, dusts, powders, liquids, and buildup of material after or during use. The designations of limited-combustible and liquid materials are provided to further the scope of materials within this standard. Spray processes that occur outside without any form of an enclosure, are exempt from this standard. Application environments with acceptable ventilation systems, as defined in this standard, will control and confine spray material to safe locations. In addition, these systems are to be designed to regulate combustible particulate residue and overspray.
Proper maintenance and handling, automated or manual, of flammable or combustible materials, as defined in this standard, limits the risk of fire or explosion. Constant supervision and consideration while handling and storing, as well as consideration into storing practices, support a safe spray environment. Design of appropriate protection systems alongside personnel training in case of emergency, has the potential to limit the spread of fire and reducing loss due to damages.
NFPA 86
Standard for Ovens and Furnaces
NFPA 86 minimizes fire and explosion hazards of ovens and furnaces used for commercial and industrial processing of materials.
Summary:
The current, 2019 edition of this standard delves into the requirements for ovens and furnaces to operate within safe conditions. Building off existing NFPA, ANSI, API, ASME, ASTM, CGA, and IEG documents, this standard establishes requirements of ovens and furnaces for minimum risk of fire or explosion. This applies to Class A, Class B, Class C, and Class D ovens as well as furnaces, and any heated system for processing material. Currently existing equipment, alterations to existing equipment, and new installations are all covered within this standard. Consideration into design, location, and operating systems, as laid out in this standard, limits the risk of fire or explosion during operation. The design and criteria for explosion relief outline optimal performance with respects to furnace specifications.
Proper maintenance and design of protection measures, as defined within this standard, limits the risk of fire or explosion. Design of appropriate protection systems alongside personnel training in case of emergency, has the potential to limit the spread of fire and reducing loss due to damages. The latter sections of this standard illustrate the specific set up and maintenance for furnaces, ovens, and heating systems for processing material.
U.F.C. UNIFIED FACILITIES CRITERIA
UFC 3-410-04 Industrial Ventilation
https://www.wbdg.org/ffc/dod/unified-facilities-criteria-ufc/ufc-3-410-04
Summary:
The UFC is a system applied for the military departments that regard planning, design, construction, sustainment, restoration, and modernization criteria. The UFC 3-410-04, Industrial Ventilation 2017 document supersedes UFC 3-410-04N, Industrial Ventilation 2004. This UFC provides the specifications for the design of the ventilation system used for the generated particulates from industrial processes. The criteria in this UFC should be treated as the minimum requirements and use the most current edition of standards. This UFC specifically address asbestos, delagging, torpedo refurbishing, composites fabrication and repair. This document applies to all service elements and contractors that are involved in the planning, design, and construction of Department of Defense facilities worldwide. The general building requirements must comply with UFC 1-200-01, DoD Building Code.
Specified in this document include general requirements, asbestos delagging facilities, otto fuel ii facilities, composite fabrication and repair facilities, abrasive blasting facilities, wood shop facilities, battery maintenance facilities, paint spray booths and aircraft corrosion control hangars.
U.F.C. UNIFIED FACILITIES CRITERIA
UFC 4-211-01 Aircraft Maintenance Hangars, with change 2
https://www.wbdg.org/ffc/dod/unified-facilities-criteria-ufc/ufc-4-211-01
Summary:
The UFC is a system applied for the military departments that regard planning, design, construction, sustainment, restoration, and modernization criteria. The UFC 4-211-01, Aircraft Maintenance Hangars 2017 supersedes UFC-4-211-01N, Aircraft Maintenance Hangars: Type 1, Type 2 and Type 3 dated 25 October 2004 with change 3 dated 16 December 2009. This document provides the criteria for planning and design of Aircraft Maintenance Hangars for aircraft of the Department of Defense and Unites States Armed Forces. The information contained in this document are applied to all new projects including additions, altercations, and renovation projects in the United States. This document specifies requirements for aircraft hangars that support all fixed wing, rotary wing, and hybrid aircraft of the United States Army, Air Force, Navy, Marine Corps, and Reserves. Unmanned Aircraft Systems or Remotely Piloted Aircraft also apply. This document applies to all aircraft hangars including maintenance hangars and other specialized hangars such as depot, transient, special operations, research, fuel-cell maintenance, and prototype.
Specified in this document include planning and layout, General Hangar Requirements, Emerging Aircraft, Air Force Specific Criteria, Army Specific Criteria, and Navy Specific Criteria. Each branch of the United States Armed Forces Criterions include sections for civil, architectural, structural, mechanical, fire protection and life safety, electrical, overhead bridge cranes. Hangar doors, floors and trench drains, fuel cell maintenance hangars, wash bay, facilities for unfueled aircraft, and hangars for fuel servicing.
U.F.C. UNIFIED FACILITIES CRITERIA
UFC 4-211-02 Aircraft Corrosion Control and Paint Facilities
https://www.wbdg.org/ffc/dod/unified-facilities-criteria-ufc/ufc-4-211-02
Summary:
The UFC is a system applied for the military departments that regard planning, design, construction, sustainment, restoration, and modernization criteria. The UFC 4-211-02 2012, Aircraft Corrosion Control and Paint Facilities supersedes the UFC 4-211-02NF Corrosion Control and Paint Finishing Hangars dated January 2005. This document provides the required specifications for evaluating, planning, programming, and designing Aircraft Corrosion and Paint Facilities. Aircraft Corrosion and Paint Facilities provide an area with structured and supported infrastructure intended for a space to paint, de-paint, and apply corrosion control related operations for the aircraft. The Building requirements are to comply with UFC 1-200-01, General Building Requirements. The information in this criteria applies to additions, altercations, and renovation projects in the United States. These requirements apply to Army, Navy, Marine Corps and Air Force facilities unless specified otherwise. This document was developed to provide design requirements to assist planners in understanding the facility requirements to provide accurate space programs and budgets as well as provide architects, engineers, and construction surveillance personnel with the minimum requirements for the design of Aircraft Corrosion Control or Paint Finishing Facilities.
Specified in this document are planning and layout, general design criteria, media blast hangar design criteria, chemical depaint design criteria, aircraft wash racks, and specific design criteria.
ANSI Z83.4-2017/CSA 3.7-2017
Non-Recirculating Direct Gas-Fired Heating and Forced Ventilation Appliances For Commercial and Industrial Application
https://webstore.ansi.org/Standards/CSA/ANSIZ832017CSA
Summary:
The current, 2017 edition of this standard delves into heating and non-forced ventilation appliances used within commercial and industrial environments. This standard applies to newly created non-recirculating direct gas-fired heating as well as forced ventilation processes. The heaters covered in this standard, draw air directly from outdoors or through a direct source to the outdoors. Pertaining to commercial and industrial applications, areas with sleeping quarters are exempt from this standard. Heaters design to produce an air temperature larger than 160 F (71 C), are also exempt from this standard. Unique or standalone production heaters are not covered within this standard. Installation of these heaters shall conform with local building regulations or National Fuel Gas Code, ANSI Z223.1/NFPA 54, or CSA B149.1 when no local regulations are in place.
ANSI Z83.18-2017
Recirculating Direct Gas-Fired Heating And Forced Ventilation Appliances For Commercial And Industrial Applications
https://webstore.ansi.org/Standards/CSA/ANSIZ83182017
Summary:
The current, 2017 edition of this standard delves into recirculating direct gas-fired heating and forced ventilation appliances used in commercial and industrial applications. This standard applies to newly created recirculating direct gas-fired heating and forced ventilation appliances for use in building heating and ventilation. The heaters and appliances covered in this standard, are to draw air directly from outdoors or through a direct source to the outdoors. Recirculating air may vented into the system, before or following the combustion zone. Heaters design to produce an air temperature larger than 160 F (71 C), are exempt from this standard. Unique or standalone production heaters are not covered within this standard.
ANSI Z83.25-2017/CSA 3.19-2017
Direct Gas-Fired Process Air Heaters
https://webstore.ansi.org/Standards/CSA/ANSIZ83252017CSA19
Summary:
The current, 2017 edition of this standard delves into direct gas-fired process air heaters used in commercial or industrial applications. This standard applies to process air heaters that utilize recirculating or non-recirculating air, in application to heat non-occupied areas or as a non-recirculating ventilation heater during times where the application space is occupied. Heaters operating at discharge temperature greater than 250 F (121 C) are exempt from this standard. Pertaining to commercial and industrial applications, areas with sleeping quarters are exempt from this standard. Installation of these heaters shall conform with local building regulations or National Fuel Gas Code, ANSI Z223.1, or CAN/CSA B149.1 when no local regulations are in place. Unique or standalone production heaters are not covered within this standard.
During periods of occupied application zones, heaters are to conform to the ventilation air heater application provisions, as defined within this standard. During the bake cycle mode, by-products created from the heater are not covered within this standard as this operation mode is only intended for periods when the application zones are non-occupied. While functioning as a paint booth heater and during the spraying applications, heaters are to be operated as non-recirculating ventilation air heaters. While operating within bake or drying mode, heaters may operate as a recirculating heater if the conditions laid out in section 4.1, 4.15, and 4.21 are met.
ACGIH
American Conference of Governmental Industrial Hygienist
Summary:
The first edition of this manual was first used in 1951 by engineers, regulators, and industrial hygienists to design and evaluate industrial ventilation systems. Throughout the years, the Industrial Ventilation manual has been updated accordingly with subsequent additions of chapters on organization and evaluation of systems, metric solutions and tables, and calculation sheets and methods. This manual includes the topics of risk assessment, preliminary design and cost estimation, principles of airflow, industrial ventilation system design principles, duct system and discharge stack design principles, hood design, fans, air cleaning devices, local exhaust ventilation system design calculation procedures, general industrial ventilation, supply air systems, special topics and techniques, and specific operations.
FM Factory Mutual
Booth Guidelines
https://www.fmglobal.com/research-and-resources/standards-and-certification
Summary:
FM Global works with government authorities, research institutions and advocacy groups to promote and enable safer requirements for clients by preventing costly losses of property. FM Global is established as a major contributor to improve fire codes and regulations in the commercial and industrial markets. Its main purpose is to strengthen building codes and fire codes to benefit their clients. FM Global Property Loss Prevention Data Sheets are made to reduce the risk of property loss due to fire, weather and/or equipment failure. The guidelines set from the industry standard contain the information to understand prevention engineering and contribute to business resilience.
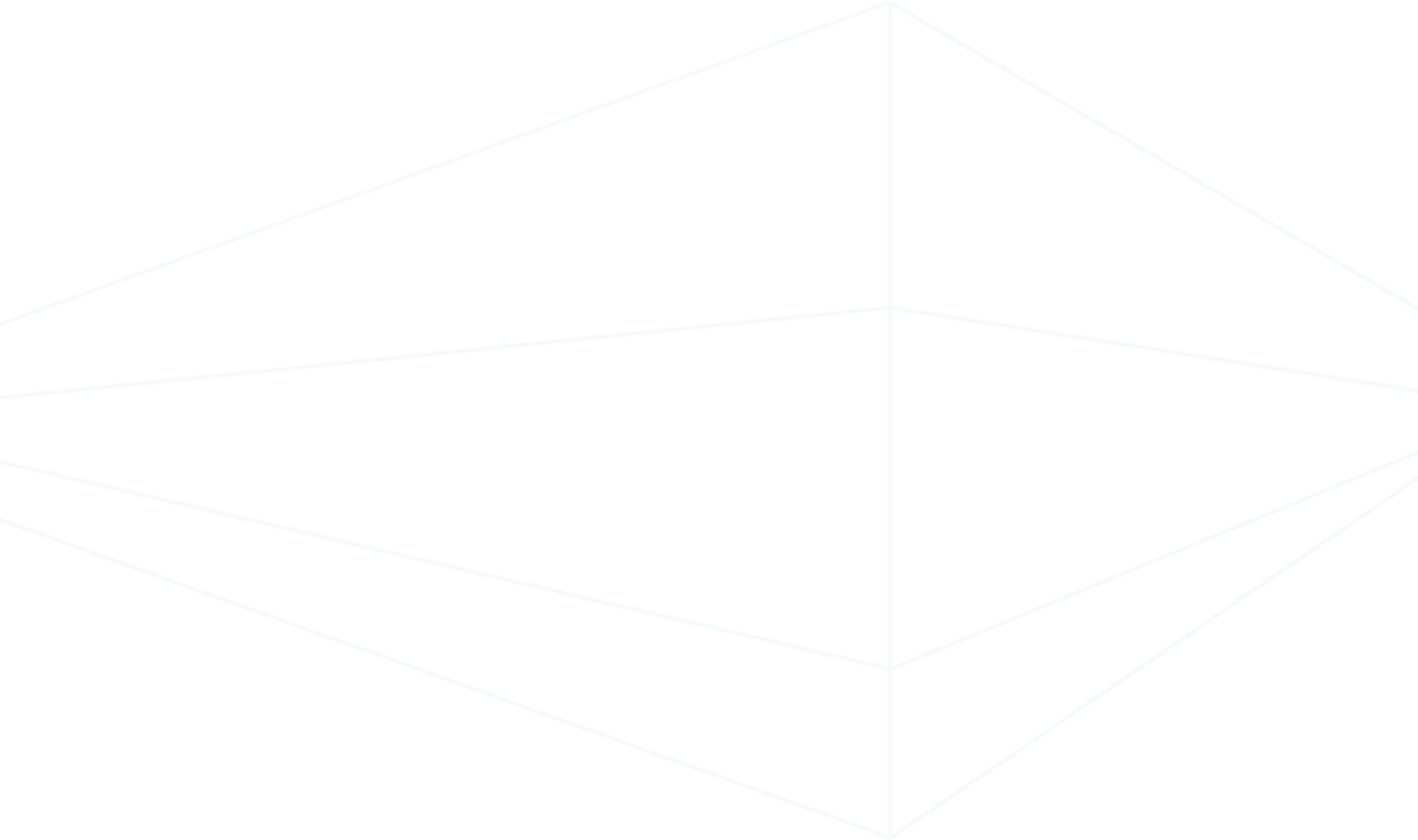